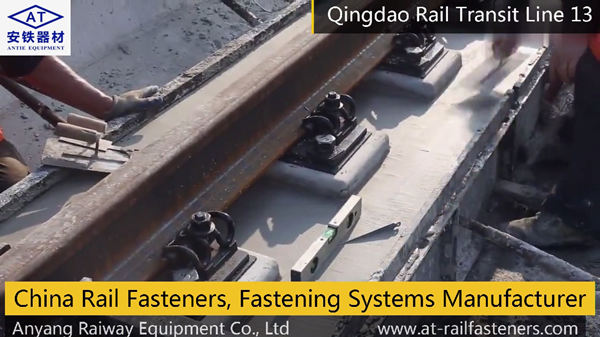
“Reinforcement Cage Rail Arrangement” Construction Technology–Qingdao Metro Line 13
The Qingdao Metro Line 13 project adopts the “reinforced cage rail arrangement” construction technology for the first time in the underground section, and the steel spring floating slab track bed is paved.
Qingdao Metro Line 13 is the fourth line completed and operated in Qingdao City, Shandong Province, China, and it is also the first subway line opened in Qingdao West Coast New Area. As of December 2018, the total length of Qingdao Metro Line 13 is 70 km.
The Qingdao Metro Line 13 project adopts the “reinforced cage rail arrangement” construction technology for the first time in the underground section, and the steel spring floating slab track bed is paved.
The steel cage rail arrangement method increases the pavement progress of the ballast bed from 25m/day for traditional manual laying to 50m/day, and can reach 75m at the fastest time. Because this process has the characteristics of mechanization and standardization, it can realize precise control of the accuracy of the ballast bed.
Innovative laying of elevated U-beam integral track bed:
In the track laying construction of the elevated U-shaped girder integral track bed, the innovative use of the “straight track laying method” overcomes construction problems such as narrow space on the bridge, slow progress of loose laying operations, low degree of mechanization, and large safety hazards, and improves construction efficiency. Labor costs are saved. Innovatively invented the automatic sleeper separation platform, which ensures the accuracy of sleeper spacing and improves the efficiency of rail row assembly.
Introduced high-speed rail CPIII track precision measurement system:
The introduction of high-speed rail CPIII track precision measurement system and track fine-tuning trolleys for alignment and elevation adjustment ensures the smooth operation of rail trains and improves the comfort of passengers.
Improve the research and development of rail material reversing trolley:
Focusing on technical research and innovation, the “Zero Point” QC activity team was established, and the upper flange plate of the U box girder was fully utilized to develop a rail material reversing trolley, which improved the progress of rail reloading and installation in the narrow space on the bridge, and reduced labor costs.