The Technology of Railway Synthetic Sleeper(Composite Sleeper)
Aug 05, 2021
The wooden sleepers erected on railway bridges have problems such as quality degradation and incomplete anti-corrosion treatment, which leads to a decline in their performance and life, which restricts the increase in operating speed, axle load and transportation volume. Today we will introduce a new type of sleeper, which is a synthetic sleeper(composite sleeper).
Wooden sleepers were widely used in the early stages of railway construction in the world. Almost all of the early railway tracks in my country used wooden sleeper structures on exposed decks. However, there are many shortcomings exposed in the long-term application of the wooden sleepers on the exposed bridge deck, mainly including easy corrosion, easy cracking, short service life, and large quality dispersion. The general service life is only 5-10 years. The surface of the wooden sleepers has poor pressure bearing capacity and is not It is environmentally friendly, and its accessories have problems such as poor retention of fasteners, easy loosening of spikes, and easy loosening and misalignment of hook bolts. The above shortcomings have caused problems such as poor line stability of the exposed deck of the steel bridge, rapid decline in the connectivity between sleepers and the deck and rails, large dispersion, large vibration response of the bridge, and large maintenance workload.
With the continuous improvement of the existing line's operating speed, axle load and transportation volume, coupled with the increasingly scarce wood resources to meet the requirements of sleepers, a new type of composite sleeper came into being.
Composite sleeper means that glass fiber reinforced materials (fiber bundles, fiber cloths, felts), unsaturated polyester resins and auxiliary materials (catalysts, curing agents, UV absorbers, fillers, etc.) are formed by pultrusion under high temperature conditions The production line of a new type of hollow structure synthetic sleeper is shown in Figure 1. The biggest advantage of this synthetic sleeper is that it makes full use of the strength of fiber-reinforced materials and the elasticity of resin materials. Its structural layout and production process are optimized according to the stress characteristics of the sleeper, which combines the high strength of traditional concrete sleepers and the good elasticity of wooden sleepers.
Compared with wooden sleepers, synthetic sleepers have the advantages of high strength, corrosion resistance, long service life, good track gauge retention, flexible fastener installation, and mechanization and continuity of production.
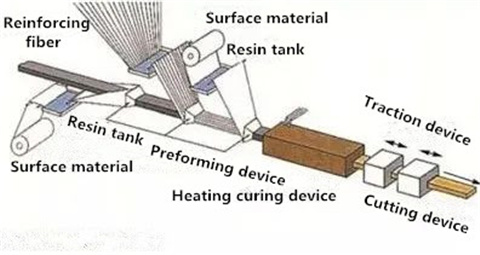
Figure 1 Synthetic sleeper pultrusion production line
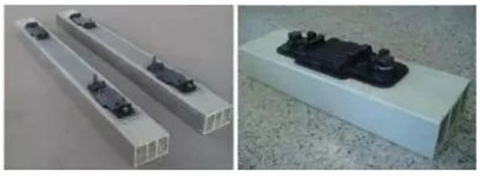
Figure 2 Synthetic sleeper fasteners
The performance parameter test of composite sleeper mainly includes body sampling performance parameter and overall strength parameter test. As there is no relevant standard for synthetic sleepers, and there is no corresponding strength standard for wooden sleepers, the test methods used in the study of synthetic sleepers are based on existing concrete sleepers and corresponding fastener standards. The cross-sectional size of the synthetic sleeper test sample is 24 cm (width) × 15 cm (height), and the unit mass is 25.54 kg/m. The sampling performance parameters and overall strength parameters are shown in Table 1 and Table 2, respectively.
Wooden sleepers were widely used in the early stages of railway construction in the world. Almost all of the early railway tracks in my country used wooden sleeper structures on exposed decks. However, there are many shortcomings exposed in the long-term application of the wooden sleepers on the exposed bridge deck, mainly including easy corrosion, easy cracking, short service life, and large quality dispersion. The general service life is only 5-10 years. The surface of the wooden sleepers has poor pressure bearing capacity and is not It is environmentally friendly, and its accessories have problems such as poor retention of fasteners, easy loosening of spikes, and easy loosening and misalignment of hook bolts. The above shortcomings have caused problems such as poor line stability of the exposed deck of the steel bridge, rapid decline in the connectivity between sleepers and the deck and rails, large dispersion, large vibration response of the bridge, and large maintenance workload.
With the continuous improvement of the existing line's operating speed, axle load and transportation volume, coupled with the increasingly scarce wood resources to meet the requirements of sleepers, a new type of composite sleeper came into being.
Composite sleeper means that glass fiber reinforced materials (fiber bundles, fiber cloths, felts), unsaturated polyester resins and auxiliary materials (catalysts, curing agents, UV absorbers, fillers, etc.) are formed by pultrusion under high temperature conditions The production line of a new type of hollow structure synthetic sleeper is shown in Figure 1. The biggest advantage of this synthetic sleeper is that it makes full use of the strength of fiber-reinforced materials and the elasticity of resin materials. Its structural layout and production process are optimized according to the stress characteristics of the sleeper, which combines the high strength of traditional concrete sleepers and the good elasticity of wooden sleepers.
Compared with wooden sleepers, synthetic sleepers have the advantages of high strength, corrosion resistance, long service life, good track gauge retention, flexible fastener installation, and mechanization and continuity of production.
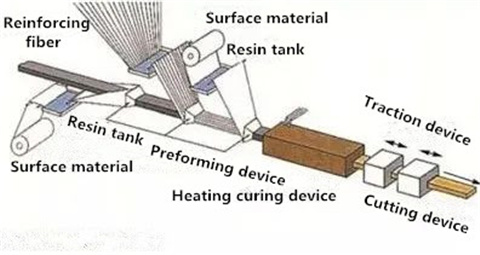
Figure 1 Synthetic sleeper pultrusion production line
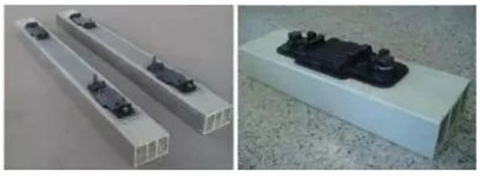
Figure 2 Synthetic sleeper fasteners
The performance parameter test of composite sleeper mainly includes body sampling performance parameter and overall strength parameter test. As there is no relevant standard for synthetic sleepers, and there is no corresponding strength standard for wooden sleepers, the test methods used in the study of synthetic sleepers are based on existing concrete sleepers and corresponding fastener standards. The cross-sectional size of the synthetic sleeper test sample is 24 cm (width) × 15 cm (height), and the unit mass is 25.54 kg/m. The sampling performance parameters and overall strength parameters are shown in Table 1 and Table 2, respectively.
Table 1 Sampling performance parameters of the synthetic sleeper body | |||
Item | Index requirements | Test Data | Test Standard |
Shear strength between layers/MPa | ≥30 | 40. 2 | GB/T 1450. 1—2005 |
Impact toughness/MPa | ≥30 | 37. 7 | GB/T 1451—2005 |
Bending strength/MPa | ≥250 | 578 | GB/T 1449—2005 |
Flexural modulus/GPa | ≥20 | 40. 7 | GB/T 1449—2005 |
Tensile Strength/MPa | ≥250 | 470 | GB/T 1447—2005 |
Tension modulus/GPa | ≥20 | 44. 7 | GB/T 1447—2005 |
Density/(g.cm-3) | 1. 8~2.0 | 1.91 |
Table 2 Overall strength parameters of synthetic sleepers | |||
Test items | Index requirements/kN | Test Data | Test Standard |
Fatigue strength | 185/37 | 2xl06 times without brakeage | TB/T 1879—2002 |
Failure load | >250 | 600 ~ 650 | TB/T 1879—2002 |
Screw spike pull-out strength | >80 | 100~140 | Q/CR 352—2016 |
Fastener assembly fatigue | 80/20 | 2xl06 times without brakeage | TB/T 2491—94 |
126/25 | 3xl06 times without brakeage | TB/T 3396.4—2015 |
|
Note: The values before and after ''/'' are the maximum and minimum loading amplitudes. |
The mechanical performance indicators of synthetic sleepers are much higher than wooden sleepers, and some indicators are even better than those of concrete sleepers. Compared with wooden sleepers, its various indicators can be quantitatively analyzed and inspected, and the quality of industrialized finished products is consistent.
.jpg)
Figure 4 Cross section of synthetic sleeper
.jpg)
Figure 4 Cross section of synthetic sleeper
Table 3 Cross-section parameters of synthetic sleepers | ||||||
Sleeper type | Section Size/ (cmXcm) | E/GPa | Ix/cm4 | F/cm2 | Sx/cm3 | Ymax/cm |
Synthetic Sleeper 1 | 24X15 | 40 | 4 035 | 134 | 337 | 7.64 |
Synthetic Sleeper 2 | 24x17 | 40 | 5519 | 143 | 406 | 8.67 |
Wooden Sleeper | 20x24 | 9 | 23 040 | 480 | 1 440 | 1.20 |
Note: E is the flexural modulus of elasticity; IX is the moment of inertia; F is the section trifoliate: S*x is the static moment: Ymax is the maximum distance between the neutral axis and the bottom of the section. The force distribution of the track structure is basically within the range of 5 sleepers, and the stress conditions of the 5 sleeper rails under failure and normal conditions are analyzed: ①Every sleeper has 1 sleeper failure (that is, 3 sleepers share the wheel weight) ②All sleepers can work normally (that is, 5 sleepers share the wheel weight). The new lead screw nut is made of high-performance engineering plastic iglidur J200. In the igus test laboratory, the service life of the nut made of this new material running on the hard anodized aluminum screw is three times longer than that of the nut made of the standard nut material under the same working conditions. When used with an aluminum lead screw, this new type of engineering plastic nut can reduce noise, reduce vibration, and is lighter. It is very common in the door systems of trains and airplanes, as well as applications in the field of logistics handling and automation. Cylindrical and flanged screw nuts are in stock, which are suitable for large-pitch threaded screws and self-locking trapezoidal threaded screws. |
.jpg)
Figure 5 The force distribution of different numbers of sleepers
Synthetic sleeper 2 has the same flexural rigidity as the wooden sleeper, and can be used as the best size for alternative wood. Considering the installation problems with fasteners, longitudinal beams and hook bolts, the cross-sectional form of the composite sleeper is optimized (Figure 6), and bottom ribs are added for the installation of sleeper bottom brackets.
Synthetic sleeper 2 has the same flexural rigidity as the wooden sleeper, and can be used as the best size for alternative wood. Considering the installation problems with fasteners, longitudinal beams and hook bolts, the cross-sectional form of the composite sleeper is optimized (Figure 6), and bottom ribs are added for the installation of sleeper bottom brackets.
.jpg)
Figure 6 Design optimization of cross-section of synthetic sleeper
The wooden sleepers on the exposed deck of the steel bridge use K-type fasteners, which are non-shoulder structural fasteners. Therefore, synthetic sleepers also use this type of fasteners. Typical non-shoulder fasteners include WJ-7 type, DT-Ⅱ type fasteners, etc., which have the characteristics of large buckling force, good elasticity, and strong track gauge retention ability. The composite sleeper is a hollow structure with a constant cross section, and an iron backing plate with a supporting rail groove can be installed on the sleeper. The Chinese Academy of Railway Sciences Group Co., Ltd. developed MQ-1 type fasteners for the synthetic sleepers and the wooden sleepers on the exposed bridge deck (Figure 7). The hollow structure of the sleepers is fully utilized in the design of the fastener connection. Female, used to fix the anchor bolts connected with the iron backing plate.
The wooden sleepers on the exposed deck of the steel bridge use K-type fasteners, which are non-shoulder structural fasteners. Therefore, synthetic sleepers also use this type of fasteners. Typical non-shoulder fasteners include WJ-7 type, DT-Ⅱ type fasteners, etc., which have the characteristics of large buckling force, good elasticity, and strong track gauge retention ability. The composite sleeper is a hollow structure with a constant cross section, and an iron backing plate with a supporting rail groove can be installed on the sleeper. The Chinese Academy of Railway Sciences Group Co., Ltd. developed MQ-1 type fasteners for the synthetic sleepers and the wooden sleepers on the exposed bridge deck (Figure 7). The hollow structure of the sleepers is fully utilized in the design of the fastener connection. Female, used to fix the anchor bolts connected with the iron backing plate.
.jpg)
Figure 7 MQ-1 type fastener installation schematic (unit: mm)
Since the exposed surface of the steel bridge is equipped with pre-camber, vertical and horizontal beam horizontal bolts, anti-climbing angle steel, etc., the installation height of sleepers at different positions of the longitudinal beams is also different. For wooden sleepers, grooves are generally carved at the bottom, and the groove depth and position of the grooves are adjusted to meet the requirements of different installation positions. Under the premise of meeting the requirements of strength and deflection, the cross-sectional size of the composite sleeper is relatively small, so there is enough space to adjust the installation height on the existing exposed bridge. The sleeper adopts an adjustable bottom bracket standard part assembly structure (Figure 8). The bottom bracket standard parts are composed of height-adjusting pads of different thicknesses and models, and sleeper bottom brackets, which can be installed in different positions of the longitudinal beams and reduce on-site operations. quantity. The sleeper bottom support and the ribs at the bottom of the sleeper form a vertical and horizontal limit to ensure the stability of the bottom support. The synthetic sleeper can be directly installed with wooden sleeper hook bolts. If the wooden sleeper is not properly handled on site after slotting, the interior is more likely to decay, and the synthetic sleeper has no material decay problem and high compressive strength, which can effectively play the anti-rotation stop function of the hook bolt. By optimizing the installation of the hook bolts, the hollow structure has the built-in mother-of-pearl and the internal cavity to prevent the rotation of the mother-of-pearl, and the hook bolts are installed with the help of the installation process hole. This solution not only prevents the hook bolts from rotating, but also increases the protection of the bolts.
Since the exposed surface of the steel bridge is equipped with pre-camber, vertical and horizontal beam horizontal bolts, anti-climbing angle steel, etc., the installation height of sleepers at different positions of the longitudinal beams is also different. For wooden sleepers, grooves are generally carved at the bottom, and the groove depth and position of the grooves are adjusted to meet the requirements of different installation positions. Under the premise of meeting the requirements of strength and deflection, the cross-sectional size of the composite sleeper is relatively small, so there is enough space to adjust the installation height on the existing exposed bridge. The sleeper adopts an adjustable bottom bracket standard part assembly structure (Figure 8). The bottom bracket standard parts are composed of height-adjusting pads of different thicknesses and models, and sleeper bottom brackets, which can be installed in different positions of the longitudinal beams and reduce on-site operations. quantity. The sleeper bottom support and the ribs at the bottom of the sleeper form a vertical and horizontal limit to ensure the stability of the bottom support. The synthetic sleeper can be directly installed with wooden sleeper hook bolts. If the wooden sleeper is not properly handled on site after slotting, the interior is more likely to decay, and the synthetic sleeper has no material decay problem and high compressive strength, which can effectively play the anti-rotation stop function of the hook bolt. By optimizing the installation of the hook bolts, the hollow structure has the built-in mother-of-pearl and the internal cavity to prevent the rotation of the mother-of-pearl, and the hook bolts are installed with the help of the installation process hole. This solution not only prevents the hook bolts from rotating, but also increases the protection of the bolts.
.jpg)
Figure 8 Synthetic sleeper bottom support combination
Conclusion: The strength indicators of composite sleepers are far superior to wooden sleepers, and can be tested by quantitative indicators. Their service life and quality consistency have greater advantages over wooden sleepers. As a new application in the railway field, Synthetic sleepers(composite sleeper) will surely become railways in the future. Mainstream products for the renewal of sleepers.