Hot-Dip Galvanized Production Line for Railway Rail Fasteners
Jun 05, 2021
What is Hot-Dip Galvanized?
The process and method of immersing pre-treated steel or cast iron parts in a molten zinc bath to form zinc and/or zinc-iron alloy coatings on their surfaces. The steel piece itself is used as the base material, and the melting point of the coating should be lower than the melting point of steel (1538°C). Since the standard electrode potential of zinc is negative than that of iron, the galvanized layer has the function of sacrificing anode to protect the steel base in water and humid air, which can greatly prolong the service life of the steel. ) Other commonly used coating metals, aluminum (melting point 658.7℃), tin (melting point 231.9℃), lead (melting point 327.4℃)
Hot-Dip Galvanized Theory?
When the metal workpiece is immersed in molten zinc, a solid solution of zinc and α iron (body-centered) is first formed at the interface. This is a crystal formed by dissolving zinc atoms in the base metal iron in a solid state. The two metal atoms are fused, and the attraction between the atoms is relatively small. Therefore, when zinc reaches saturation in the solid solution, the atoms of the new two elements diffuse into each other, and the zinc atoms diffused into (or infiltrated) the iron matrix migrate in the crystal lattice, and gradually form alloys with iron, which diffuses The iron in the zinc solution forms the metal compound FeZn13 with zinc, and sinks into the bottom of the hot-dip galvanizing pot, which is the zinc slag. When the workpiece is removed from the zinc immersion solution, a pure zinc layer is formed on the surface, which is a hexagonal crystal. Its iron content is not more than 0.003%.
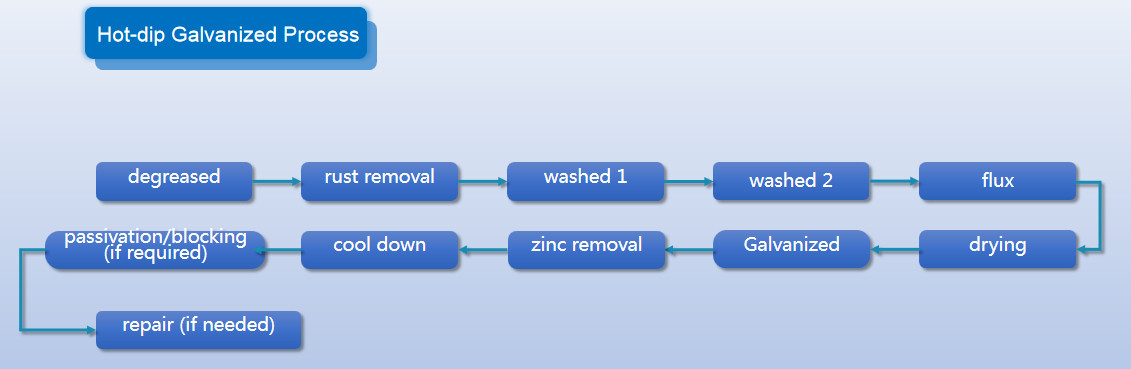
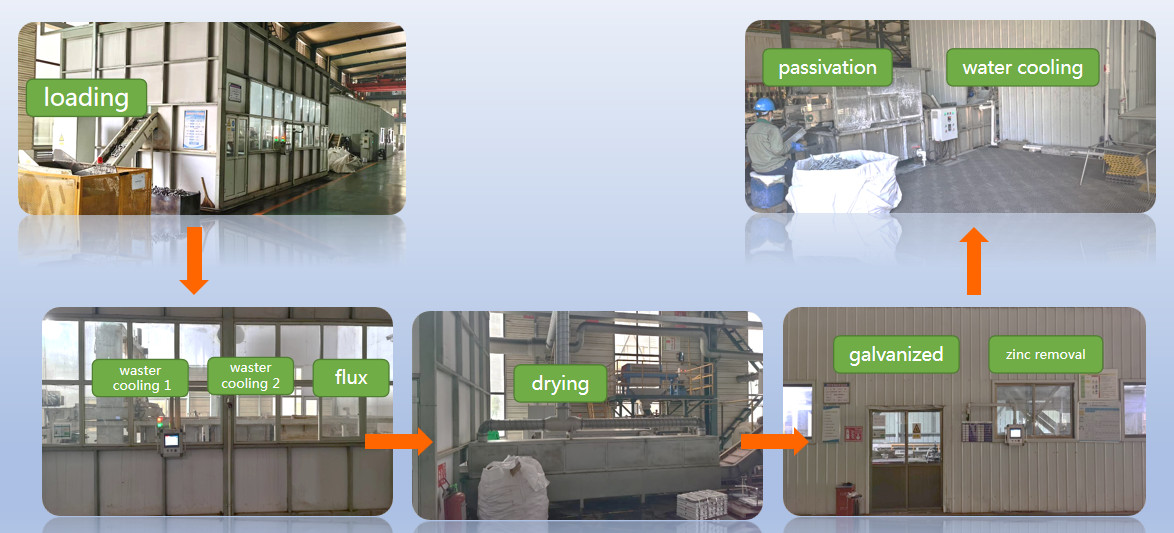
Anyang Railway Equipment Co., Ltd(AT) has modern Hot Galvanized Production Line, which is used for railway rail fixing infractructure materials such as rail bolts, washers, nuts, screw spikes, rail gauge apron plates, rail clips, etc. The maximum output is 20 t/day.
.jpg)
The process and method of immersing pre-treated steel or cast iron parts in a molten zinc bath to form zinc and/or zinc-iron alloy coatings on their surfaces. The steel piece itself is used as the base material, and the melting point of the coating should be lower than the melting point of steel (1538°C). Since the standard electrode potential of zinc is negative than that of iron, the galvanized layer has the function of sacrificing anode to protect the steel base in water and humid air, which can greatly prolong the service life of the steel. ) Other commonly used coating metals, aluminum (melting point 658.7℃), tin (melting point 231.9℃), lead (melting point 327.4℃)
Hot-Dip Galvanized Theory?
When the metal workpiece is immersed in molten zinc, a solid solution of zinc and α iron (body-centered) is first formed at the interface. This is a crystal formed by dissolving zinc atoms in the base metal iron in a solid state. The two metal atoms are fused, and the attraction between the atoms is relatively small. Therefore, when zinc reaches saturation in the solid solution, the atoms of the new two elements diffuse into each other, and the zinc atoms diffused into (or infiltrated) the iron matrix migrate in the crystal lattice, and gradually form alloys with iron, which diffuses The iron in the zinc solution forms the metal compound FeZn13 with zinc, and sinks into the bottom of the hot-dip galvanizing pot, which is the zinc slag. When the workpiece is removed from the zinc immersion solution, a pure zinc layer is formed on the surface, which is a hexagonal crystal. Its iron content is not more than 0.003%.
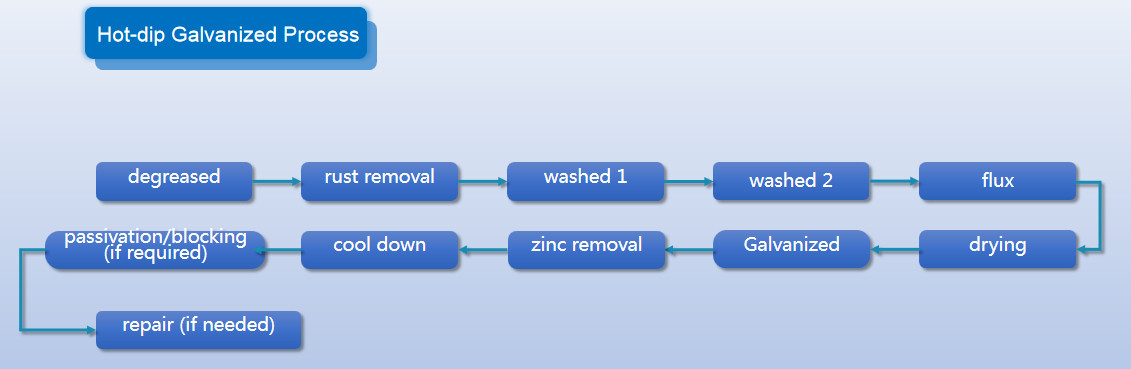
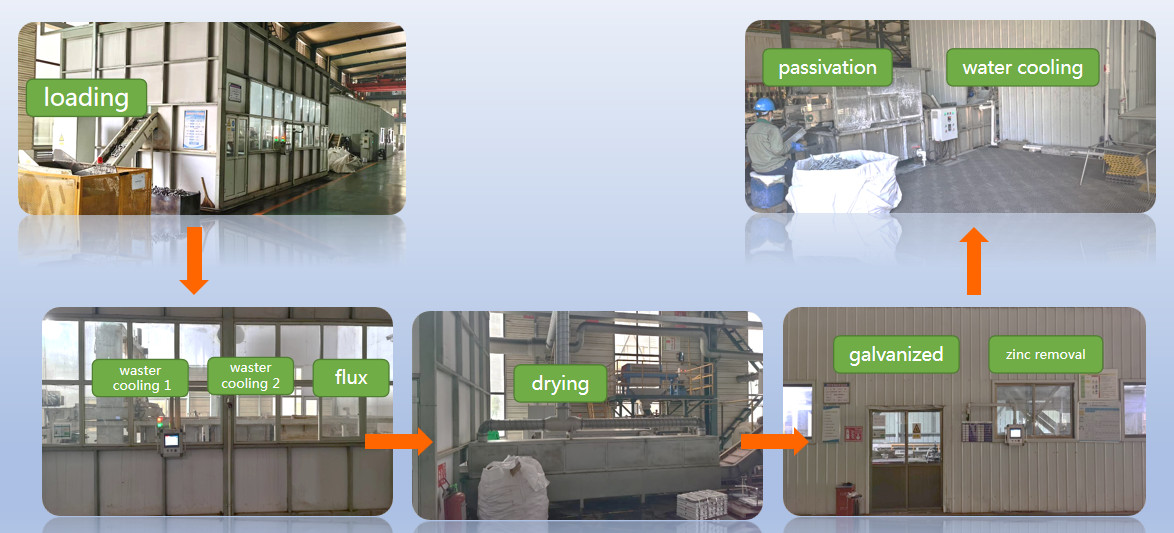
Anyang Railway Equipment Co., Ltd(AT) has modern Hot Galvanized Production Line, which is used for railway rail fixing infractructure materials such as rail bolts, washers, nuts, screw spikes, rail gauge apron plates, rail clips, etc. The maximum output is 20 t/day.
.jpg)