Composite for Timber-Replacement Bearer in Railway Switches, Crossings
Aug 06, 2021
1. Introduction
Railway urban turnout is a special track system used to divert a train from a particular direction or a particular track onto other directions or other tracks. It is a structural grillage system that consists of steel rails, points (or called switches'), crossings (special track components), steel plates, rubber pads, insulators, fasteners, screw spikes, beam bearers (either timber, polymer, steel, or concrete), ballast, and formation, as shown in Figure 1 . Traditional turnout structures were generally supported by timber bearers. The timber bearers allow the steelwork to be mounted directly on steel plates that are spiked or screwed into the bearers. Timber, steel, and concrete are common materials, which have had long history records of usage in tracks over a decade. Timber has an excellent damping coefficient, whilst concrete and steel tend to have almost no damping coefficient. Concrete has proven to be an excellent counterpart to improve track and turnout stability—laterally, longitudinally, and vertically. Recent studies also show that steel bearers perform well in a short term, but have higher turnout settlement and ballast breakage over the long term.
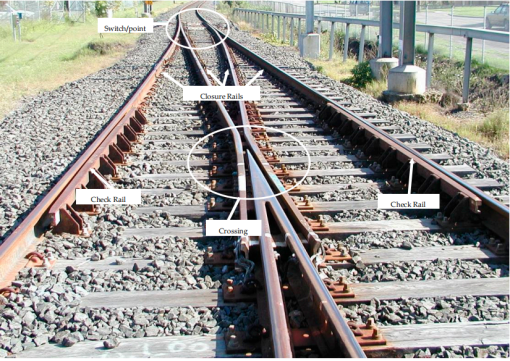
Figure 1. Typical turnout geometry
2. Materials and Methods
It is well known that traditional turnout generally imparts high impact forces on to structural members because of its blunt geometry and mechanical connections between closure rails and switch rails (i.e., heel-block joints).
Currently, the procurement of high-quality long timber bearers used in complex turnout systems is very difficult for either construction or renewal processes in Australia. Problems with long timber turnout bearers (>4 m) include localised weakness]argedeformation, warping, or unstable dimensions that can easily cause obstructions during the turnout assembly resulting in a poor geometry or new turnouts. Then, the wheel/rail interaction (see Figure 2) over such poor short-pitch irregularity induces impact force and vibration that exacerbates the condition and undermines the service life of turnout components and the integrity of turnout system as a whole.
.png)
Figure 2. Transfer zone at crossing where a conical wheel traversing
Railway urban turnout is a special track system used to divert a train from a particular direction or a particular track onto other directions or other tracks. It is a structural grillage system that consists of steel rails, points (or called switches'), crossings (special track components), steel plates, rubber pads, insulators, fasteners, screw spikes, beam bearers (either timber, polymer, steel, or concrete), ballast, and formation, as shown in Figure 1 . Traditional turnout structures were generally supported by timber bearers. The timber bearers allow the steelwork to be mounted directly on steel plates that are spiked or screwed into the bearers. Timber, steel, and concrete are common materials, which have had long history records of usage in tracks over a decade. Timber has an excellent damping coefficient, whilst concrete and steel tend to have almost no damping coefficient. Concrete has proven to be an excellent counterpart to improve track and turnout stability—laterally, longitudinally, and vertically. Recent studies also show that steel bearers perform well in a short term, but have higher turnout settlement and ballast breakage over the long term.
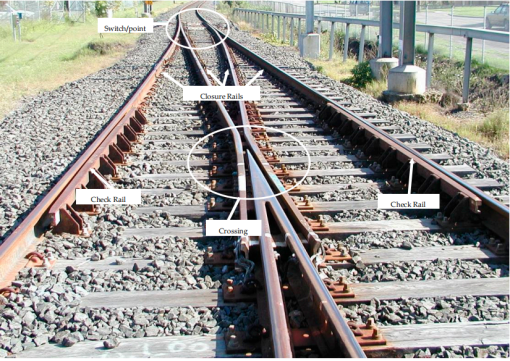
Figure 1. Typical turnout geometry
2. Materials and Methods
It is well known that traditional turnout generally imparts high impact forces on to structural members because of its blunt geometry and mechanical connections between closure rails and switch rails (i.e., heel-block joints).
Currently, the procurement of high-quality long timber bearers used in complex turnout systems is very difficult for either construction or renewal processes in Australia. Problems with long timber turnout bearers (>4 m) include localised weakness]argedeformation, warping, or unstable dimensions that can easily cause obstructions during the turnout assembly resulting in a poor geometry or new turnouts. Then, the wheel/rail interaction (see Figure 2) over such poor short-pitch irregularity induces impact force and vibration that exacerbates the condition and undermines the service life of turnout components and the integrity of turnout system as a whole.
.png)
Figure 2. Transfer zone at crossing where a conical wheel traversing
Table 3. Basic properties of Synthetic material in comparison with timber bearers
Properties | Australian Hardwood Bearers | Birch (Softwood) Bearers | Synthetic Material Bearers | |||
New | After 10 Years | After 15 Years | After 30 Years | |||
Service life (years) | 5-10 | 5-10 | 50 | 40 | 35 | 20 |
Density (kg/m3) | 1050-1120 | 750 | 740 | 740 | 740 | 740 |
Bending strength (MPa) > 70 | 65 | 80 | 142 | 125 | 131 | 116 |
Vertical compression strength (MPa) > 40 | 60 | 40 | 58 | 66 | 63 | 55 |
Shear strength (MPa) > 7 | 6.1 | 12 | 10 | 9.5 | 9.6 | 7 |
Elastic modulus (MPa) > 6000 | 16,000 | 7100 | 8100 | 8044 | 8788 | 8414 |
Fatigue flexural strength | 50,000 cycles at 40 MPa | 50,000 cycles at 40 MPa | 1 million cycles at 94 MPa | |||
Hardness (MPa) | 10 | 17 | 28 | 25 | 17 | |
Water absorption (mg/cm2) <10 | 137 | 137 | 3.3 | 3.3 | 3.3 | 3.3 |
Impact bending strength (MPa) | ||||||
@20℃ | - | 20 | 41 | - | - | - |
@-20℃ | - | 8 | 41 | - | - | - |
Destructive voltage (kV) | ||||||
- dry (>20,000) | 8 | 8 | >25 | >25 | >25 | >25 |
-wet (>20,000) | <1 | <1 | 22 | 24 | 23 | 25 |
Insulation resistance (Ω) | ||||||
-dry (>1.0 x 104) | 6.6 x 107 | 6.6 x 107 | 1.6 x 1013 | 2.1 x 1012 | 3.6 x 1012 | 8.2 x 1011 |
-wet (>1.0 x 104) | 5.9 x 104 | 5.9 x 104 | 1.4 x 108 | 5.9 x 1010 | 1.9 x 109 | - |
Dog spike pull-out strength (kN) > 15 | 25 | 25 | 28 | 28 | 23 | 22 |
Screw spike pull-out strength (kN) > 30 | 40 | 43 | 65 | 39 | 44 | 33 |
Timber bearer properties are derived from AS1720 Strength Group 2. Birch timber bearer properties are derived from the technical datasheet. This timber is equivalent to soft wood.
3.Materials Sensitivity
Since the beginning of the history of railways, timber is the main and most used material for sleepers. Due to a scarcity of noble wood, the high price, and increased maintenance requirements, the need for other materials has grown. Concrete and steel have emerged as options for new lines. Mechanical advantages and lower susceptibility to wear are the major appealing features presented by steel and concrete sleepers. However, they do not have mechanical properties compatible with the timber sleeper, making ineffective the replacement and co-operation. Therefore new timber sleepers still are a more favorable option in a short term to replace the damaged sleepers in existing lines.
3.1. Timber
A major advantage of timber sleepers is their flexibility, which results in a great ability to resist vibrations deriving from dynamic loads in railway track systems. The ease of handling, replacement, and adaptation to track systems are other benefits of this material.
Timber sleepers can be suited to all types of railway track. Additionally, the electrical isolation provided by a timber sleeper is valuable to the signaling system and only plastic or fiber composites sleepers could also match this characteristic. Esveld arranged timber sleepers into two categories: softwood (e.g., pinewood) and hardwood (e.g., beech, oak, tropical tree). Hardwood timber is the most common sleeper material in railway lines through the world. Its advantages over the softwood timber are its greatest strength and durability. However, over the years the hardwood timber has become increasingly expensive, its availability is reducing and those which are still available no longer have the same quality.
Although more resistant to fungal decay, softwood sleepers offer less resistance to end splitting, gauge spreading, and spike hole enlargement than hardwood sleepers. Furthermore, they are less effective in transmitting loads to the ballast section as hardwood sleepers. Due to this difference in loads transmission hardwood sleepers and softwood sleepers should not be used together on the railway track. Due to diverse environmental conditions, woods are susceptible to severe degradation due to the attack of various organisms. The resistance of untreated wood to fungal decay in service above ground is low, affecting its durability. Non-durable timbers generally require preservative treatment if they are to be used in exposed conditions, adding significantly to their cost. Moreover, there is growing concern regarding the use and disposal of this impregnated material for their consequences for the environment.
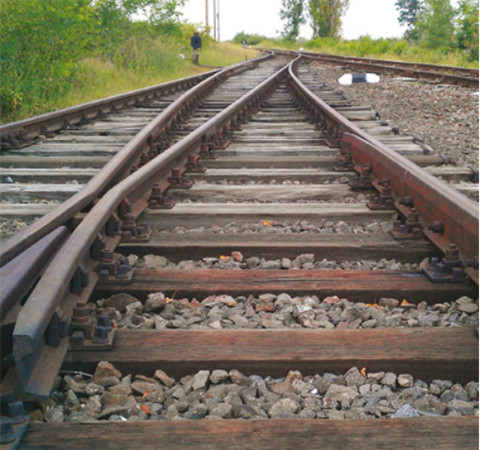
3.2. Concrete
After the Second World War, the use of concrete sleepers had a significant increase in Britain and Europe due to timber scarcity. Progressively, reinforced and pre-stressed concrete sleepers have replaced timber and steel sleepers due to their prolonged life cycle and reduced maintenance costs. Two varieties of concrete sleepers are offered in the market: reinforced twin-block and prestressed monoblock sleepers. The twin-block consists of two blocks of reinforced concrete connected by a steel bar or stiff steel beam. While monoblock sleepers consist of one prestressing reinforced concrete beam. The monoblock concrete sleeper is the type that has greater acceptance in the market due to its superior durability in the face of unfavourable environments. Another advantage observed is the resistance to twists, failure commonly presented by twin block concrete sleepers. Because of this usual failure, the installing process of this type of sleeper requires greater care, making it more difficult to handle and contributing to a lower acceptance, even with their reduced weight compared to monoblock sleepers.
Concrete is known for its high resistance to compression, on the other hand, it presents weakness when it comes to tension. Due to this characteristic, monoblock concrete sleepers use the technique of prestressing to withstand the dynamic loads arising from the passage of the train. This procedure consists of the tensioning of steel rods before or after the concrete is molded. Prestressed concrete presents increased ductility, higher flexural strength, and resistance to cracking. The stability and slight position movement offered by prestressed concrete sleepers because of its heavyweight meant that it had a significant acceptance in high-speed lines. At the same time, the great weight reduces mobility, making it difficult to transport and being necessary specific equipment for installation which increases the costs of concrete sleepers. One of the causes of this high weight is a need for greater thicknesses in comparison to timber sleepers with the aim of reducing dynamic tension at the bottom fiber costs for producing and maintaining prestressed concrete sleepers are considerably elevated. Their initial costs are about twice that of the hardwood timber sleepers. However, due to its high durability and specifications that comply with the solicitations of a railway system, prestressed concrete sleepers can be currently considered as the best cost-benefit to serve ballasted railway lines and the preferred sleeper to railway tracks nowadays.
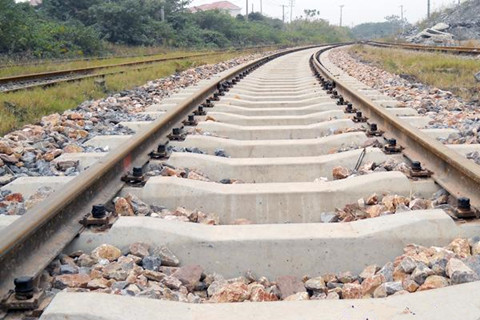
3.3. Steel
With a typical lifecycle of about 50 years, steel sleepers emerged as a first option to substitute timber sleepers around the 1880s. A steel sleeper presents higher mechanical strength, can be lighter than timber, and are easy to handle, they can even be operated manually. However, their use is usually limited to lightly traveled tracks. An excellent gauge restrains and increased lateral resistance due to its geometry are other technical advantages presented by a steel sleeper. Additionally, damaged sleepers also have commercial value, since the steel can be recycled several times and reused in the railway industry. In the search for further improving the characteristics of steel sleepers, the traditional orthogonal sleepers have been replaced by Y-steel-sleepers (Figure 3). The development of this new model provided a further reduction in weight of steel sleepers and gain of resistance against cross movements due to the amount of accumulated ballast in its central part as a consequence of its design similar to the letter Y.
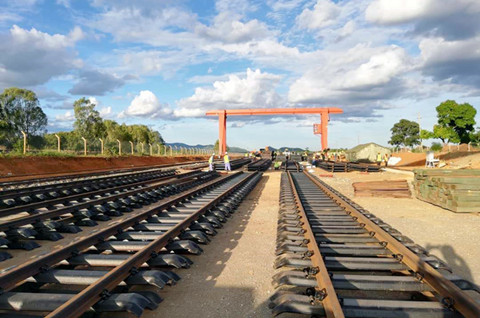
Figure 3. Y-Steel-Sleeper
The construction industry is one of the greatest consumers of raw material and energy, as well as a major generator of environmental pollution. The manufacturing process of railway sleepers can be associated with substantial environmental impacts. Resource required to the production of sleepers as energy and material are responsible for a large greenhouse gas emission. Materials such as concrete and steel consume a significant amount of energy during production and could dispense respectively 10–200 times more carbon dioxide into the atmosphere than hardwood timber sleepers. Moreover, gases are also generated during the transportation and installation of sleepers and a great quantity of waste is resulted, mostly from the harvesting of timber. However, during the service life, the decay of timber sleepers continues resulting in impacts to the environment.
This is due to the fact that during their growth, trees keep in its structure carbon that is absorbed from the atmosphere, and once the timber has been cropped it progressively liberates carbon dioxide back to the environment. Then this emission is extending even after the disposal of these sleepers until the end of its decomposition. One research founded that emissions related to the service life of timber sleepers can be up to six times greater than the emissions associated with reinforced concrete sleepers. Another concern related to using and discarding of timber sleepers comes from the practice of chemically impregnating them with creosote to preserves it from biological deterioration.
Despite being widely used, toxic substances are present in these chemical preservatives which do not easily decompose in nature and are volatiles. So they are gradually released into the air during the life cycle of the sleeper and may cause environmental pollution and present risks to human health. On the other hand, plastic sleeper, when made from recycled plastic, can be beneficial to the environment. Its production not only saves the use of other materials but also provides functionality to a considerable amount of waste as well as attaching commercial value to a material that would be discarded. Though, the use of non-recycled plastic for manufacturing sleepers generates concerns mainly because of some plastics being a by-product of oil, in addition to being non-biodegradable. Furthermore, the service life of the sleepers has a great impact on its sustainability since it determines the demand of material over the years, and also the amount of discarded units, which generates a great impact especially on the use of land. The expected service lives of the different types of sleepers are listed on Table 4.
Table 4. Expected Life Cycle of Different Type of Railway Sleepers
Material | Service Life(Years) | Material | Service Life(Years) |
Timber | 15-25 | Steel | 20-30 |
Concrete | 50 | Plastic/Polymer | Over 50 |
A significant disadvantage of steel sleepers is due to difficulty to achieve reasonable packing with ballast, requiring special care during the installation process and tamping. Other problems such as fear of corrosion, fatigue cracking in the fastening holes caused by moving trains, high electrical conductivity (that can lead to problems with track circuit signaling), and excessive noise also contribute to the inferior popularity of steel sleepers. However, the greatest restriction of the use of steel as a material for the production of sleepers is its excessive value.
3.4. Plastic, Polymer, and Composites
Material scarcity, as well as environmental concern, motivates researchers regarding new materials capable of satisfying the railway system requirements. Develop a structure that is economically competitive and that meets the needs of the industry is a major challenge of civil engineering. There is a constant search for a material that is durable, reasonably easy to produce and maintain, has attractive costs, and meets the expected requests effectively. A key concern in the railway industry is the replacement of damaged and deteriorated sleepers in existing tracks. The importance of the development of the polymer and composite sleepers is due to the capacity to design them to mimic the timber behavior, which cannot be achieved with concrete and steel sleepers. A factor of extreme importance tor the maintenance of timber tracks. Moreover, polymer and composite sleepers require low to almost no maintenance, thus this improved life-cycle makes them a suitable alternative for areas that are harder to maintain such as tunnels, bridges, and turnouts. Another advantage is its sustainable approach, which makes them be notable in the face of the constant increase of concern over the existing environment in the current industry.
Many studies are given in the area of polymers and composites as materials for the manufacture of sleepers. A composite material is manufactured from two or more distinct materials combined to achieve characteristics not found in those who compose it. There are several efforts towards improving the characteristics of the materials already used in the railway track engineering (wood, steel, and concrete) as applied to the polymer by itself or composite polymers, using mainly fibers. A fiber composites system characteristically consists of a lightweight polymer matrix with strong fibers inserted into it. The fiber reinforcement sustains the load due to its high strength and can be applied as reinforcement only in the longitudinal direction or longitudinal and transverse directions.
Fiber composites could be perfectly suitable for the production of railway sleepers. These composite can be engineered based on the required structural applications and manufactured with almost the same dimensions and weight as that of hardwood timber. Additionally, fiber composites railway sleepers offer high strength, are light, and present a longer lifecycle, reducing maintenance costs. Moreover, fiber composites are easy to handle, they can be drilled in situ for the connection of the fastener system and inserted under the track as timber sleepers. Another appeal of polymer and composites sleepers is the environmental question. There are many efforts in study polymers produced from recycled plastic. Since 1990, several U.S. companies and institutions have shown interest in the production of sleepers from recycled plastic. The recycled plastic material can help reduce emissions of greenhouse gas, save millions of trees, reduce chemical contamination due to the preservatives present in timber sleepers, and also add commercial value to a large amount of waste. Economically most fiber composite sleeper developments still have disadvantages compared to traditional sleeper materials due to higher initial costs.
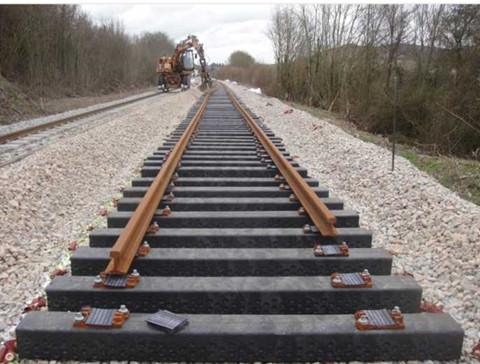
4. Systems Requirements
3.4. Plastic, Polymer, and Composites
Material scarcity, as well as environmental concern, motivates researchers regarding new materials capable of satisfying the railway system requirements. Develop a structure that is economically competitive and that meets the needs of the industry is a major challenge of civil engineering. There is a constant search for a material that is durable, reasonably easy to produce and maintain, has attractive costs, and meets the expected requests effectively. A key concern in the railway industry is the replacement of damaged and deteriorated sleepers in existing tracks. The importance of the development of the polymer and composite sleepers is due to the capacity to design them to mimic the timber behavior, which cannot be achieved with concrete and steel sleepers. A factor of extreme importance tor the maintenance of timber tracks. Moreover, polymer and composite sleepers require low to almost no maintenance, thus this improved life-cycle makes them a suitable alternative for areas that are harder to maintain such as tunnels, bridges, and turnouts. Another advantage is its sustainable approach, which makes them be notable in the face of the constant increase of concern over the existing environment in the current industry.
Many studies are given in the area of polymers and composites as materials for the manufacture of sleepers. A composite material is manufactured from two or more distinct materials combined to achieve characteristics not found in those who compose it. There are several efforts towards improving the characteristics of the materials already used in the railway track engineering (wood, steel, and concrete) as applied to the polymer by itself or composite polymers, using mainly fibers. A fiber composites system characteristically consists of a lightweight polymer matrix with strong fibers inserted into it. The fiber reinforcement sustains the load due to its high strength and can be applied as reinforcement only in the longitudinal direction or longitudinal and transverse directions.
Fiber composites could be perfectly suitable for the production of railway sleepers. These composite can be engineered based on the required structural applications and manufactured with almost the same dimensions and weight as that of hardwood timber. Additionally, fiber composites railway sleepers offer high strength, are light, and present a longer lifecycle, reducing maintenance costs. Moreover, fiber composites are easy to handle, they can be drilled in situ for the connection of the fastener system and inserted under the track as timber sleepers. Another appeal of polymer and composites sleepers is the environmental question. There are many efforts in study polymers produced from recycled plastic. Since 1990, several U.S. companies and institutions have shown interest in the production of sleepers from recycled plastic. The recycled plastic material can help reduce emissions of greenhouse gas, save millions of trees, reduce chemical contamination due to the preservatives present in timber sleepers, and also add commercial value to a large amount of waste. Economically most fiber composite sleeper developments still have disadvantages compared to traditional sleeper materials due to higher initial costs.
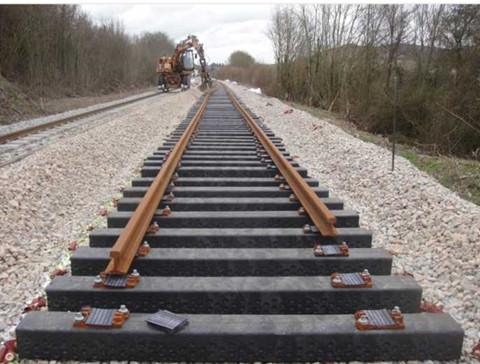
Both the sleepers in the mainline and the bearers in switches and crossings are the safety-critical components for railway applications. As the essential part of the rail track systems, the main requirements of sleepers and bearers include providing an anchorage for the fastening system, keeping the stability of railway track, and transmission vertical, lateral and longitudinal loads from the rails to the ballast or other support. In real-life practices around the world, they are also exposed to the sun (UV radiation), rainfall, frost damage (freeze and thaw), elevated temperature (ambient, hot trackwork such as grinding and welding), and so on. These various exposures require railway sleepers and bearers to provide sufficient durability and ductility. Based on these inevitable criteria, all of the sleepers and bears made by different materials should meet the systems requirements suitable for different types, local parameters, and locations of railway tracks.
They must meet the safety and maintenance targets set by the local rail authorities or infrastructure managers. International Union of Railway (UIC) has classified the railway track into five different categories in European countries (as shown in Table 7). The track engineers and sleeper designers must consider the design parameters set for each category.
.png)
Compared with the commonly used material (concrete), the composite sleepers could have similar and different mechanical characteristics. Concrete sleepers manufactured in different countries have similar strength, stability, and durability, but different kinds of composite sleepers (manufactured by different companies) have totally different engineering properties and resultant behaviors in the field. Depending on whether they are reinforced or not, composite sleepers can be classified into unreinforced sleepers and reinforced sleepers. Based on the polymer type, the composite sleepers can be classified into thermoplastics sleepers and thermosetting sleepers as well. Since there are different kinds of reinforcement (fibrous materials, GFRP, steel bars and high-strength steel wires), the composite sleepers could still have other classification methods such as by its reinforcement or by its compositions (cement-based matrix, brittle resin, or plastic resin). There are many kinds of composite sleepers developed around the world, and these sleepers might present longer life cycles and friends to the environment, but they also have some critical deficiencies. Some composite sleepers lose the fastening systems caused by creep deformation; some composite sleepers crack early due to voids inside the materials that concentrate the applied load; some composite sleepers made by recycled plastic sleepers expand obviously when the temperature changes are excessive; some composite sleeper degenerated rapidly explored to the environment (due to UV radiation, moisture et al.); and there are some other kinds of composite sleepers do not have enough lateral resistance.
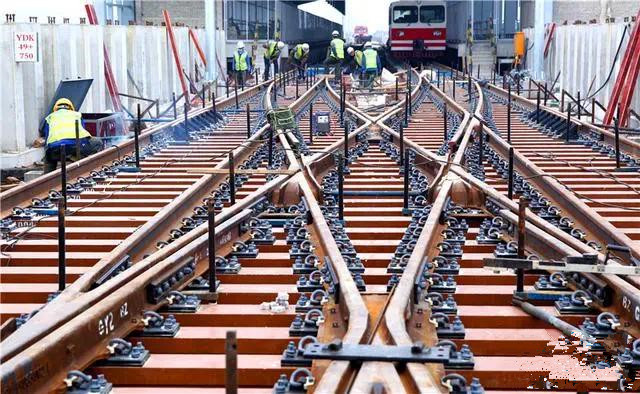
Usually, railway tracks could be designed up to 50 years with regular routine maintenance. However, bearers could have pre-mature failure due to irregularities. The replacement or modification of the turnout bearers requires an appropriate structural design principle in assuring that safety margin and structural reliability can be retained without undermining long-term sustainability requirements of each rail authority. These also mean that it is highly necessary to optimize their own material characteristics of specific composite sleepers or bearers. It is also very critical that the sleepers or bearers provide assured capability to resist repetitive loading and provide sufficient durability.
They must meet the safety and maintenance targets set by the local rail authorities or infrastructure managers. International Union of Railway (UIC) has classified the railway track into five different categories in European countries (as shown in Table 7). The track engineers and sleeper designers must consider the design parameters set for each category.
.png)
Compared with the commonly used material (concrete), the composite sleepers could have similar and different mechanical characteristics. Concrete sleepers manufactured in different countries have similar strength, stability, and durability, but different kinds of composite sleepers (manufactured by different companies) have totally different engineering properties and resultant behaviors in the field. Depending on whether they are reinforced or not, composite sleepers can be classified into unreinforced sleepers and reinforced sleepers. Based on the polymer type, the composite sleepers can be classified into thermoplastics sleepers and thermosetting sleepers as well. Since there are different kinds of reinforcement (fibrous materials, GFRP, steel bars and high-strength steel wires), the composite sleepers could still have other classification methods such as by its reinforcement or by its compositions (cement-based matrix, brittle resin, or plastic resin). There are many kinds of composite sleepers developed around the world, and these sleepers might present longer life cycles and friends to the environment, but they also have some critical deficiencies. Some composite sleepers lose the fastening systems caused by creep deformation; some composite sleepers crack early due to voids inside the materials that concentrate the applied load; some composite sleepers made by recycled plastic sleepers expand obviously when the temperature changes are excessive; some composite sleeper degenerated rapidly explored to the environment (due to UV radiation, moisture et al.); and there are some other kinds of composite sleepers do not have enough lateral resistance.
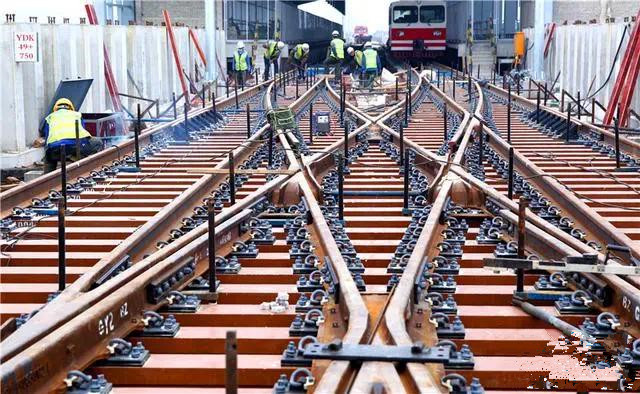
Usually, railway tracks could be designed up to 50 years with regular routine maintenance. However, bearers could have pre-mature failure due to irregularities. The replacement or modification of the turnout bearers requires an appropriate structural design principle in assuring that safety margin and structural reliability can be retained without undermining long-term sustainability requirements of each rail authority. These also mean that it is highly necessary to optimize their own material characteristics of specific composite sleepers or bearers. It is also very critical that the sleepers or bearers provide assured capability to resist repetitive loading and provide sufficient durability.